Validate and Benchmark: Measure for Success
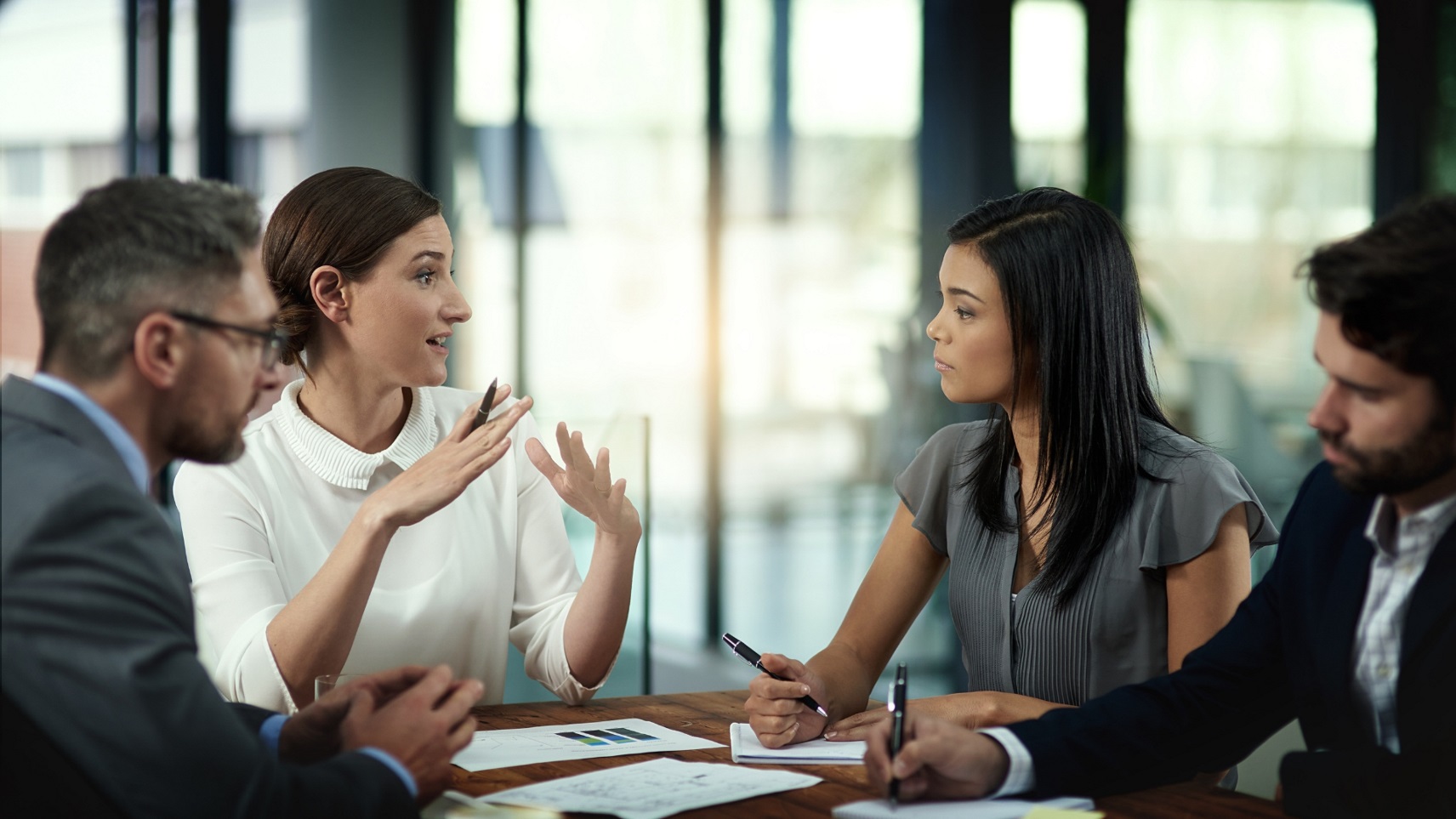
Welcome back to our Six Sigma series! In our last article, Identify Opportunities for Improvement: Define to Refine, we explored how to establish the foundation for process improvement by defining the problem and identifying key opportunities. Now, we move to the Measure Phase, where the focus shifts to gathering reliable data to validate these opportunities and set measurable benchmarks for success.
The Measure Phase is the second step in the Six Sigma DMAIC (Define, Measure, Analyze, Improve, Control) methodology. It’s a pivotal stage that ensures improvement efforts are grounded in data, not assumptions. By collecting accurate data, validating measurement systems, and establishing baseline performance, organizations can create a solid platform for data-driven decision-making.
The Importance of Validation and Benchmarking
Before diving into problem-solving, it is critical to ensure that the data used to identify and assess issues is accurate, consistent, and reliable. A lack of valid data can lead to misguided efforts, wasted resources, and missed opportunities. Benchmarking complements validation by providing a reference point, allowing teams to assess their current performance against industry standards, competitors, or internal goals.
Key Steps to Validate and Benchmark
1. Define What Needs to Be Measured
The first step is to identify the metrics that align with your objectives and critical-to-quality (CTQ) requirements. Common metrics include:
- Defect rates
- Cycle times
- Customer satisfaction scores
- Costs associated with inefficiencies
These metrics should be actionable and relevant to the project’s scope.
2. Validate Measurement Systems
Reliable data begins with a trustworthy measurement system. A Measurement System Analysis (MSA) ensures that the tools and processes used to collect data are:
- Accurate: Reflecting the true value of what is being measured.
- Consistent: Providing the same results under similar conditions.
- Reproducible: Delivering reliable outcomes across different users or scenarios.
Conducting studies like Gage R&R (Repeatability and Reproducibility) helps identify and eliminate sources of measurement error.
3. Collect and Analyze Baseline Data
Baseline data serves as the starting point for improvement. Collecting this data involves:
- Observing current processes in real time or using historical data.
- Ensuring the sample size is sufficient to represent the process accurately.
- Using tools such as control charts to determine whether the process is stable and predictable.
This data not only quantifies the problem but also highlights variability and trends.
4. Benchmark Against Standards
Benchmarking is the process of comparing your performance metrics against established standards. There are several types of benchmarking:
- Internal Benchmarking: Comparing performance across different departments or locations within the organization.
- Competitive Benchmarking: Analyzing how your performance stacks up against industry competitors.
- Best Practice Benchmarking: Studying organizations that excel in specific areas, regardless of industry, to identify practices that can be adapted.
These benchmarks provide context for your performance and help set realistic improvement targets.
5. Map and Understand the Process
A clear understanding of the process is essential for identifying improvement opportunities. Tools like SIPOC diagrams (Suppliers, Inputs, Process, Outputs, Customers) and process flowcharts help visualize workflows. Mapping the process reveals:
- Value-added versus non-value-added activities.
- Bottlenecks, delays, or waste.
- Areas of variation that contribute to defects or inefficiencies.
6. Analyze Process Capability
Assessing process capability ensures that your system can meet customer requirements consistently. Key indicators include:
- Cp: Process capability, which measures how well a process fits within specification limits.
- Cpk: Process capability index, which evaluates the centering of the process within the limits.
- Sigma Level: A measure of the process's defect rate.
These insights allow you to understand how far the current performance is from desired outcomes.
7. Validate Baseline Performance
Finally, summarize and validate the baseline performance of your process. This involves:
- Ensuring that the collected data is comprehensive and error-free.
- Using statistical tools to confirm the stability and capability of the process.
- Communicating findings with stakeholders to align on priorities for the next phase.
The Role of Validation and Benchmarking in Long-Term Success
Validation and benchmarking are not one-time activities; they are integral to fostering a culture of continuous improvement. By consistently validating data and benchmarking performance, organizations can:
- Identify gaps and opportunities with clarity.
- Avoid pursuing initiatives based on inaccurate assumptions.
- Monitor progress effectively and celebrate successes.
The Measure phase is the cornerstone of any successful Six Sigma project. By validating your measurement systems and benchmarking against relevant standards, you establish a clear and accurate foundation for improvement. These steps ensure that every subsequent action is rooted in facts, not assumptions, and set the stage for driving meaningful, sustainable change. In the end, the adage holds true: "What gets measured, gets improved."