Understanding the Basics of Process Improvement: Why It Matters
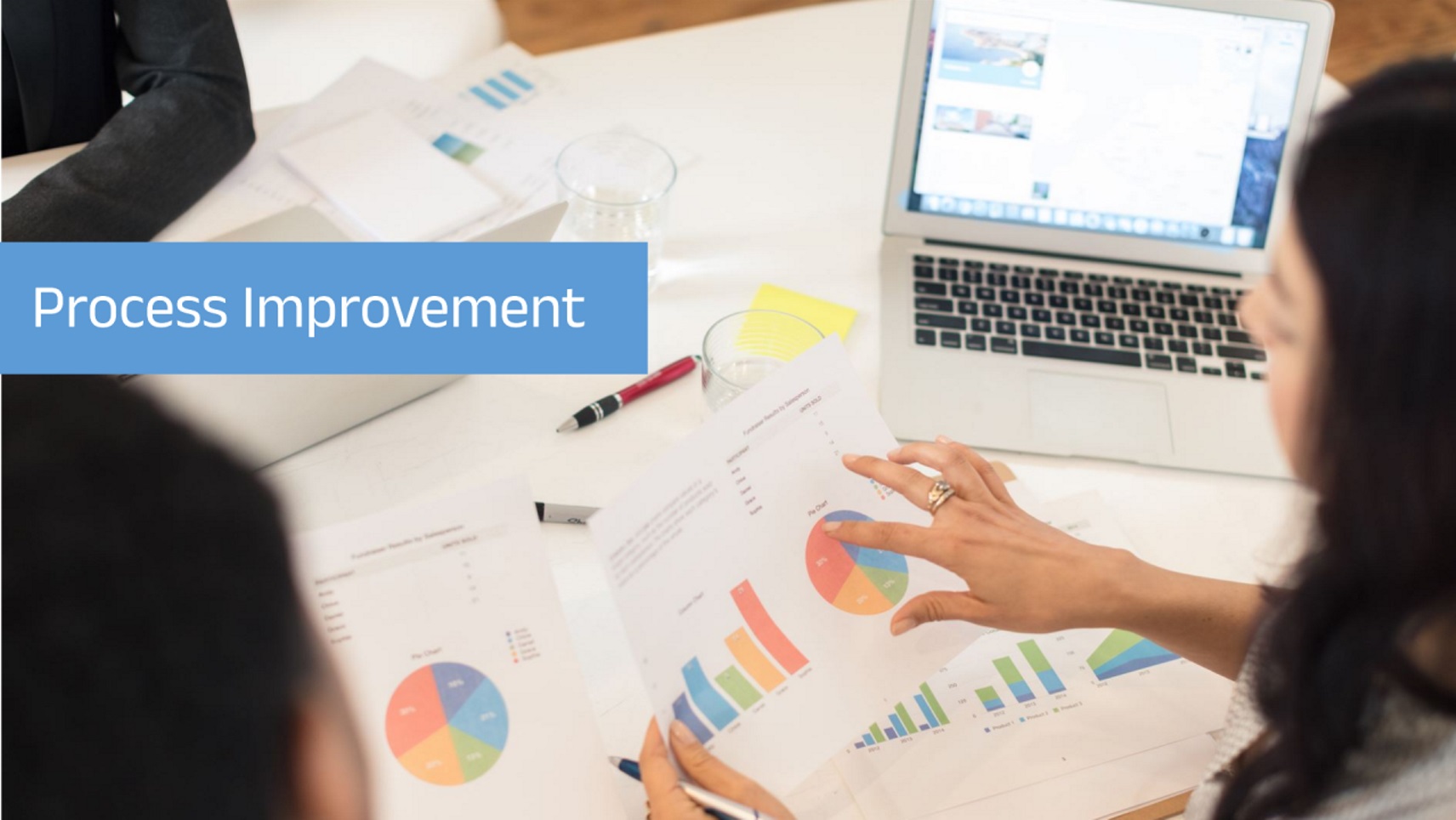
In today’s rapidly evolving business environment, efficiency, adaptability, and quality are essential to staying competitive. Companies that embrace Process Improvement are better positioned to meet these challenges by optimizing how they deliver value to customers. But what exactly is process improvement, and why should every organization make it a priority? In this article, we’ll explore the fundamentals of process improvement, its significance, and its potential to transform any business.
What is Process Improvement?
Process improvement is the practice of analyzing existing workflows, identifying inefficiencies, and making adjustments to boost productivity, quality, and speed. It’s about systematically reducing waste, improving accuracy, and making sure processes are consistent and scalable.
Several methodologies, such as Lean and Six Sigma, provide structured approaches to process improvement:
- Lean focuses on maximizing customer value by eliminating waste—any activity that doesn’t directly add value from the customer’s perspective. This approach was popularized by James P. Womack and Daniel T. Jones in their influential book, "Lean Thinking: Banish Waste and Create Wealth in Your Corporation".
- Six Sigma targets quality by minimizing defects and reducing variability in processes. As outlined in "The Six Sigma Handbook" by Thomas Pyzdek and Paul Keller, Six Sigma employs data-driven techniques and statistical analysis to drive continuous improvement and quality control.
Together, these frameworks empower organizations to systematically address inefficiencies and build a culture of continuous improvement.
Why Process Improvement Matters
- Enhanced Efficiency and Productivity. Streamlining processes means doing more with less. By removing redundant steps and automating repetitive tasks, teams can focus on activities that directly contribute to organizational goals, boosting productivity and reducing costs.
- Improved Quality and Consistency. Process improvement minimizes errors, ensuring products or services meet quality standards consistently. Six Sigma, in particular, is known for its emphasis on quality control, which reduces defects and customer complaints, as explained by the American Society for Quality (ASQ).
- Cost Reduction. Many businesses experience hidden costs from inefficient processes. By refining workflows, companies can reduce wasteful spending and streamline resource allocation.
- Agility and Adaptability. In a changing business landscape, organizations need to be agile. Process improvement makes it easier to adapt to shifting demands, new regulations, and technological advancements.
- Employee Engagement and Satisfaction. Involving employees in process improvement empowers them to take ownership of their work, leading to higher engagement and job satisfaction. Employees who see their efforts making a positive impact on the organization are more motivated and committed.
Key Steps in the Process Improvement Cycle
The process improvement cycle is a structured approach that ensures changes are meaningful and sustainable. Here’s a basic outline:
- Identify Opportunities for Improvement. Start by analyzing current workflows to find pain points and inefficiencies.
- Analyze and Measure Current Performance. Use metrics to understand the current state. For example, Lean and Six Sigma often track cycle time, defect rate, and customer satisfaction.
- Design and Implement Solutions Develop targeted improvements, such as removing bottlenecks, consolidating steps, or automating manual tasks.
- Monitor and Measure Results Measure the impact of your improvements using data-driven insights, as outlined in the Six Sigma methodology. Control charts and statistical analysis can help assess the effectiveness of changes.
- Sustain and Standardize Document and standardize successful improvements to ensure lasting benefits and make it easier to scale solutions across the organization.
Real-World Example of Process Improvement
Consider a finance department struggling with month-end closing delays due to manual data entry and fragmented communication. Through a process improvement initiative, they map out their workflows, identify bottlenecks, and introduce automation tools to handle data entry and notifications. By the next quarter, they’ve cut their close process in half—from ten days to five—freeing up team capacity for higher-value work.
Further Reading
For readers interested in diving deeper into process improvement, these resources provide valuable insights and practical guidance:
- Lean Thinking: Banish Waste and Create Wealth in Your Corporation by James P. Womack and Daniel T. Jones. This foundational book explains Lean principles and how they can transform workflows across various industries by focusing on customer value and waste elimination.
- The Six Sigma Handbook: A Complete Guide for Green Belts, Black Belts, and Managers at All Levels by Thomas Pyzdek and Paul Keller. A comprehensive guide on Six Sigma methodologies, providing tools and techniques for process improvement, quality control, and operational excellence.
- American Society for Quality (ASQ). The ASQ website offers extensive resources on quality management, Lean, and Six Sigma, with articles, tools, and certification information. Visit asq.org to explore more.
Process improvement isn’t just about fixing what’s broken—it’s about continuously seeking ways to do things better. This commitment to improvement is a powerful driver of operational efficiency, quality, and agility. For organizations looking to stay competitive, embracing process improvement isn’t optional; it’s essential.
Stay tuned for our next article, where we’ll dive deeper into the tools and techniques that make process improvement a transformative force in today’s businesses.